Hydraulics is a fascinating principle that is used in many areas of technology. But how exactly do hydraulics work and what are they used for? In this article we will take a closer look at the basics of hydraulics and consider some application examples.
Content
Basics of hydraulics
Definition of hydraulics
In the scientific sense, hydraulics is the study of still and flowing fluids and is assigned to drive technology. The word “hydraulics” comes from the Greek and is derived from the word hydro = water. When people hear the term “oil hydraulics”, they usually think of controlling the flow of lines in a plant. Here, a special hydraulic fluid is used as the transmission medium, usually hydraulic oil.
In mechanical engineering, vehicle construction and aircraft construction, hydraulics is practically applied as a branch of physics.
The picture shows the principle of power transmission between two pistons through a liquid column. The hydraulic jack, for example, also works according to this principle. This principle is fundamental for oil hydraulics. Valves (control devices for controlling the fluid flow) are added. The drive pump is a hydraulic pump, which is driven directly by an electric motor or internal combustion engine. Alternatively, the hydraulic pump can also be driven mechanically, e.g. by a power take-off shaft.
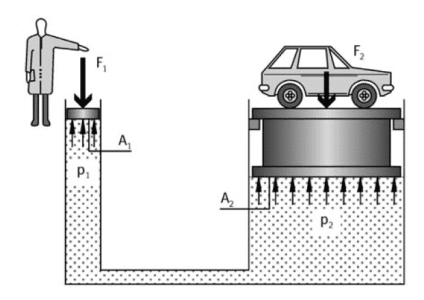
How do hydraulics work?
The operation of hydraulics is based on the principle of pressure transmission. By opening and closing hydraulic valves, the fluid flow is controlled and thus the movement of the consumer is controlled. With the help of hydraulics, high forces can be transmitted in a relatively small space. As a result, hydraulic systems are used in areas such as vehicles, mechanical engineering and industry.
Design of a hydraulic system
A hydraulic system consists of various components such as a hydraulic power unit, a hydraulic cylinder, hydraulic motors, hydraulic valves, hydraulic hose lines and a hydraulic fluid, usually hydraulic oil. By using a non-compressible fluid, pressure can be generated and transmitted. The piston of a hydraulic cylinder, for example, is moved and can thus exert a force on a load.
Difference between hydraulics and pneumatics
Similarities and differences
Both hydraulics and pneumatics work with pressure, but have different working media. While hydraulics uses a liquid as the medium, pneumatics relies on compressed air. Both systems have their advantages and disadvantages and are used in different applications.
Applications of pneumatics
Pneumatics is mainly used in areas where lower forces are required, such as in the control of production plants or test benches. However, due to the lower density of air, pneumatics are less suitable for applications with heavy loads. The (travel) speeds generated in pneumatics are much higher than in hydraulics. In PNeumatik, flow speeds of more than 20 meters per second can be achieved; in hydraulics, only 5 m/s are possible.
Application examples for a hydraulic system
Hydraulics in lifting platforms
A well-known example of the use of hydraulics are lifting platforms. Through the use of hydraulic cylinders, heavy loads can be lifted and safely positioned. The lift is controlled by a hydraulic power unit. Oil flow dividers are usually used for the synchronization of the hydraulic cylinders. For high requirements on the accuracy of synchronization, cylinders with displacement measuring systems and proportional valves with corresponding control electronics are also used.
Hydraulic drives in vehicles
Hydraulic drives are used in many vehicles, such as excavators or tractors. By using hydraulic cylinders, mechanical movements can be generated, which in turn can transmit greater forces.
Examples of applications in mobile hydraulics:
- Traction drives for work machines such as construction machinery or agricultural machinery
- Landing gear extension and wing flap control for aircraft
- Linear drives using hydraulic cylinders, e.g. for excavators or log splitters
Brake cylinder for trailers - Hydrostatic steering units (power steering systems) in construction, agricultural or municipal machinery
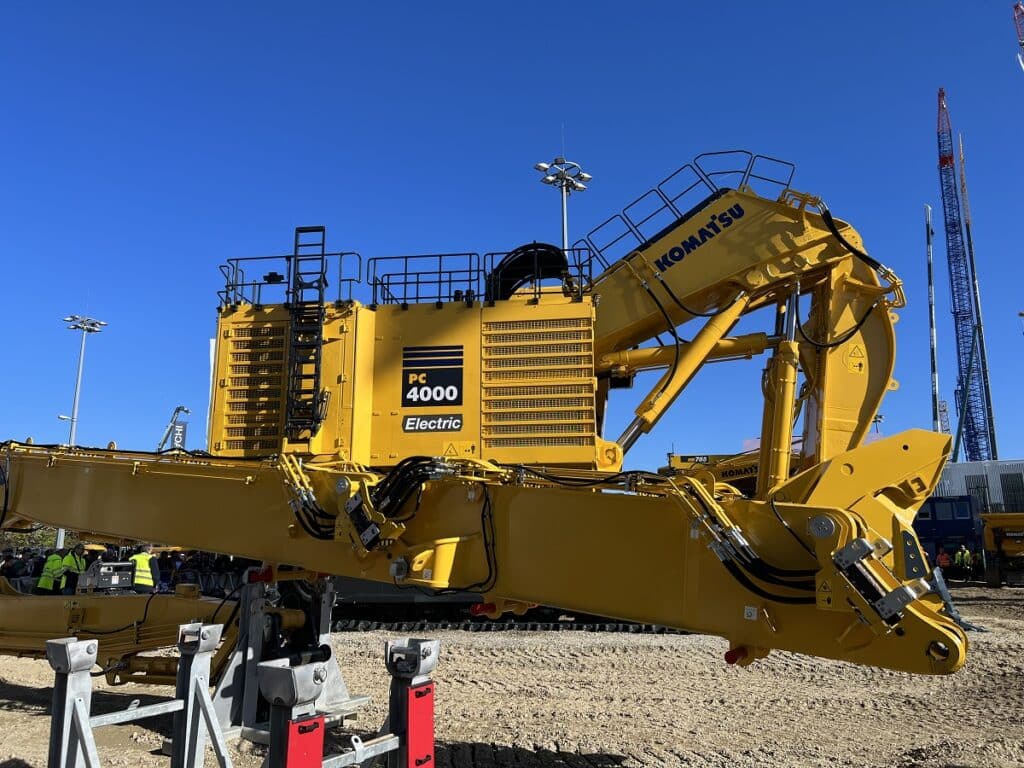
Use of hydraulics in industry
In industry, hydraulic systems find a wide range of applications. One example is the hydraulic press, which can generate enormous forces through the use of hydraulics. This enables precise and controlled shaping of workpieces.
Other examples of hydraulic applications in industry:
- Plastic injection machines
- Tube bending machines
- Assembly systems
Advantages and disadvantages of hydraulics
Hydraulics offers several advantages. By using a non-compressible fluid, pressure can be maintained, allowing high forces to be transmitted. In addition, hydraulic systems can be built relatively compactly, which saves space. Furthermore, hydraulic systems are robust and have a high load capacity. Hydraulic cylinders and especially hydraulic motors have a very high power density compared to electric motors.
Disadvantage of hydraulics
Despite the many advantages, there are also some disadvantages of hydraulics. On the one hand, hydraulic systems require regular inspection and maintenance. In addition, the hydraulic oil must be cleaned and filtered regularly to ensure smooth operation. Another disadvantage is the high energy consumption of hydraulic systems.
Vorteile | Nachteile |
---|---|
Druckflüssigkeit nicht komprimierbar, dadurch Übertragung hoher Kräfte | Regelemäßige Inspektion und Wartung notwendig |
Kompakte Bauweise | Hohe Sauberkeitsanforderungen an Hydrauliköl |
Hohe Belastbarkeit | Hydraulikanlagen können sehr komplex werden |
Hohe Leistungsdichte bei Hydraulikmotoren und Hydraulikzylindern |
Maintenance and care of hydraulic systems
Regular inspection and maintenance
To ensure a long service life and reliable operation of hydraulic systems, regular inspection and maintenance is necessary. Among other things, leakages are checked, wear parts are replaced and the system is tested for leaks.
Cleaning and filter change
Regular cleaning and replacement of filters are important measures to ensure proper functioning of the hydraulic system. Cleaning removes dirt particles that could affect the system, and filter replacement ensures good filtration of the hydraulic oil. For the requirements on oil purity, the specifications of the corresponding component manufacturers must be observed.
Preventive measures against wear
Preventive measures can be taken to prevent wear. This includes, for example, regular refilling of the hydraulic oil to ensure a sufficient supply in the reservoir. In addition, all moving parts should be regularly lubricated and checked for wear. Furthermore, it is recommended to check the cleanliness of the hydraulic oil at regular intervals. In addition to a targeted oil sample, the use of appropriate oil condition sensors is also possible.
The importance of hydraulics for modern technology
Hydraulics in the automotive industry
Hydraulics play an important role in the automotive industry. It enables, for example, the operation of car brakes or the movement of heavy loads with construction vehicles. In municipal technology, hydraulic drives are found, for example, in sweeping brooms or winter service vehicles.

Aerospace application
Hydraulics are also used in the aerospace industry. It is used, for example, to control the wing flaps on aircraft or to extend the landing gear. The hydraulics enable precise and fast movements, which are crucial for aircraft safety and control. There are also numerous applications for hydraulic components in airport apron vehicles.
Hydraulics in the mechanical engineering industry
There are numerous applications of hydraulics in the mechanical engineering industry. From hydraulic presses for shaping workpieces to the control of large machinery and equipment, hydraulics play an important role in this industry. Of course, hydraulic systems are also becoming more efficient. For example, the use of load sensing or frequency-controlled electric motors for hydraulic power units allows for a very energy-efficient use of hydraulics.
Summary
Hydraulics is a fundamental principle of engineering based on the transmission of pressure through a non-compressible fluid. The use of hydraulic systems allows high forces to be transmitted in a small space. Hydraulic systems find a wide range of applications in various sectors such as the automotive industry, mechanical engineering and industry. Advantages of hydraulics are high load capacity, compact design and the ability to move heavy loads. However, hydraulic systems require regular inspection and maintenance. In the automotive industry, aerospace and mechanical engineering, hydraulics is of great importance for modern technology.
Hydraulik in unserem Shop kaufen
- Mobile control block - 13. May 2023
- Hydraulics lowering brake valves - 6. May 2023
- axial piston engines - 2. May 2023