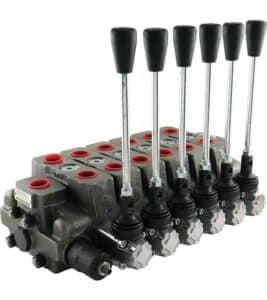
Mobile control block
In the field of mobile machinery, there are special requirements for valve technology. Control blocks for mobile applications have significant differences to hydraulic valves in
Hydraulic valves – Without valves, (almost) nothing works in a hydraulic system. It does not matter whether a consumer is to be switched, a load must be held or a control line is actuated.
Thus, hydraulic valves play a significant role in hydraulic systems as they control and regulate the flow of hydraulic oil. They are capable of controlling various functions such as start, stop, change of direction and setting the pressure or flow of the hydraulic medium. Therefore, hydraulic valves are of crucial importance for the precise and reliable functioning of hydraulic systems.
The operation of a hydraulic valve depends on the type of valve. There are two main types of hydraulic valves: Spool valves and poppet valves.
Spool valves usually use a spool as the control element. This piston moves inside a bore in the valve body. The position of the piston inside the bore determines whether the connection between the channels in the valve body is open or closed. The spool is guided in the housing with very little clearance, and the resulting liquid film between the components reduces friction (see also Brugger value). Spool valves are often used in directional control valves.
Unlike spool valves, poppet valves have a component such as a ball, plug, or disc as the control element. This component is pressed onto the valve seat by a spring to close or open the valve cover. Normally, the channel opens against the spring force when the hydraulic medium flows through. Seat valves are particularly tight compared to gate valves. For this reason, they are the preferred choice when hydraulic circuits need to be shut off without leakage. Shut-off valves such as pressure relief or check valves are examples of poppet valves.
Hydraulic valves must meet high requirements in hydraulic systems. Therefore, there are different types of hydraulic valves with different installation methods. Basically, we can distinguish types of hydraulic valves as follows:
Each installation method has specific advantages and areas of application, depending on the requirements of the hydraulic system.
In-line valves, also known as valves for in-line installation, are installed directly in hydraulic lines and serve as intermediate elements. This type of hydraulic valve has threaded connections that are attached to hydraulic pipes or hose lines with screw-in fittings.
Hydraulic valves for plate mounting can either be screwed onto a subplate (valve base plate) as a single valve or as part of a manifold plate. These valves can also be used as the top component of a vertical stacking system, for example in hydraulic power packs. As a rule, plate-mounting valves are so-called CETOP valves, which have standardized porting holes (see ISO 4401) and a standardized plate-mounting design. This allows for extremely space-saving installation. These are so-called solenoid valves.
These valves are in the form of plates that are installed between the valve base plate and the top valve of the vertical stacking system to control the hydraulic flow.
The sandwich plate valves have connection surfaces on both the top and bottom. Both connection and mounting holes are routed through the valves. This means that multiple valves can be assembled into one assembly to perform a variety of functions. As a rule, this type of valves are used for vertical interlinking.
Monobloc valves consist of a single cast block. Several valve holes are integrated in this block, through which the hydraulic oil can flow. Each of these valves can be controlled independently.
Advantage: Compared to sandwich valves, there are fewer sealing surfaces. Furthermore, there are no influences due to tie rod forces.
Disadvantage: Since they consist of a single block, a defect in one of the valves can result in the entire block having to be replaced. In addition, only a limited number of valve sections can be implemented compared to sandwich valves.
Screw-in valves are a popular solution in hydraulics for the block installation of hydraulic valves. Unlike other valve types, which are screwed onto a valve base plate or manifold plate, screw-in valves are screwed directly into the screw-in bore of the control block or housing.
The screw-in hole, also known as the cavity, contains the central mounting thread and the hydraulic connections. Depending on the design of the valve, the screw-in bore also provides corresponding sealing surfaces. Many control block manufacturers use the screw-in bore to mount hydraulic components directly in the block to minimize space requirements.
With this design, individual functions or valve plates can be combined with each other to enable a wide range of control functions in a compact assembly. Each “plate” or “slice” contains the specific function required for the various control circuits.
This type of valve is very modular, which means that they can be customized for specific applications. The valve plates are normally mounted and braced with tie rods or bolts to ensure a secure and stable construction.
These valves are often used in applications that require high flexibility and adaptability, such as mobile hydraulic applications or complex industrial hydraulic systems.
In our hydraulic store you will find a wide range of hydraulic valves. Visit us and benefit from our extensive product portfolio.
In the field of mobile machinery, there are special requirements for valve technology. Control blocks for mobile applications have significant differences to hydraulic valves in
Hydraulic lowering brake valves – safety device in hydraulic systems Counterbalance valves are hydraulic valves consisting of pilot-operated check valves and associated throttling and damping