Gerotor motor, oil motor, planetary motor - low-speed hydraulic motors
Content
How does a gerotor motor or oil motor work?
The so-called gerotor motors (also called planetary motors or simply oil motors) represent a special design of hydraulic motors. These motors work according to the planetary gear principle:
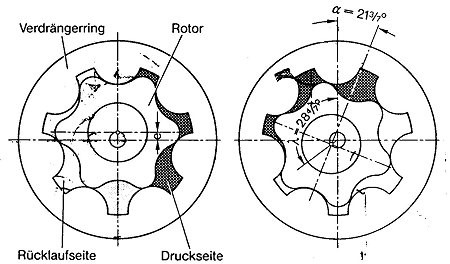
In a gerotor motor , for example, the outer ring is fixed with 7 teeth, while the inner wheel with 6 teeth performs a planetary-like movement . As a result, the volume of 6 → 7 = 42 tooth gaps is displaced during one revolution, so that a very high torque is obtained. A distinction is also made between planetary and planetary roller motors . In the case of the planetary roller motor , the inner wheel is also mounted on rollers . This achieves a better start-up behavior of the motor, as only rolling friction has to be overcome instead of sliding friction:

Gerotor motors are characterized by a large absorption volume with small device dimensions . Planetary motors are reversible (suitable for both directions of rotation) and can be operated under certain conditions without a leakage oil connection. The internal non- return valves direct the internal leakage oil to the respective low-pressure side.
Control of low-speed hydraulic motors
In the case of slow-running hydraulic motors , a distinction is made between valve control in the output shaft (drum valve) and valve control in the end cover (plate valve). Spool valves have, for example, Hydromot planetary motors of the type CPMM and CPM , as well as planetary roller motors of the type CPRM and CPMH . Poppet valves can be found in Hydromot oil motors from the CPMS series, i.e. also for CPMT and CPMV . In all gerotor motors , the distributor valve is driven synchronously with the gear set. As a result, the individual chambers of the engine are filled and emptied precisely and with almost no loss .
How does an oil motor with valve control in the output shaft work?
When hydraulic oil is applied to the front port, the oil flows through the internal bores of the hydraulic motor into the planetary gear set . The spool valve (B) is part of the output shaft . The cardan shaft (C) transmits the mechanical energy from the planetary gear set (D) to the output shaft and thus overrules the valve control .

How does a gerotor motor with valve control in the end cover work?
Heavy-duty series oil motors (Hydromot CPMS, CPM and CPMV) are controlled by a poppet valve . If port “P” is supplied with hydraulic oil, the oil flows via the poppet valve “F” through the internal bores of the motor to the planetary set (“C”). This is set in rotation. The poppet valve is separate from the output shaft (A) and is driven by a short propshaft “D” (valve propshaft). The so-called balance plate equalizes the hydraulic forces around the poppet valve and thus guarantees high efficiency. Internal non-return valves (“E”) ensure that if the leakage oil line is not connected, the leakage oil is discharged into the respective motor connection.
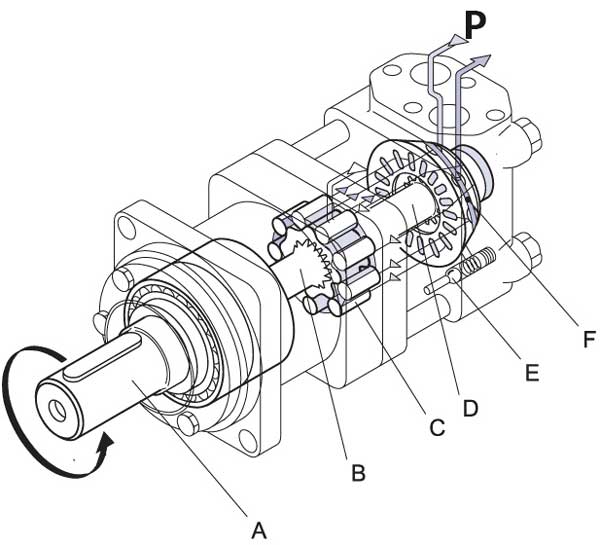
What should be considered when designing planetary motors?
If you need a replacement motor for an existing application , the choice is fairly simple. Many manufacturers are interchangeable, so that, for example, an M+S motor can also be used for a Danfoss hydraulic motor (and vice versa). Unfortunately, some machine manufacturers often do their own thing and develop special versions together with the engine manufacturer. These are often not recognizable from the outside and the type plate also does not allow any conclusions to be drawn about a special type. It can happen that the replacement engine blows in your face or does not achieve the desired performance.
What can I do to prevent this from happening and to choose the right motor?
Basically, it is always helpful to know the exact application in which the hydraulic motor is installed. This also applies to the redesign of hydraulic drives.
Basically, the following questions should be answered for the correct selection of a hydraulic motor:
- What drive power is available?
It makes sense that the existing drive power should be greater than the required power of the oil motor - Which torque or which output power is required? What delivery pressure and delivery volume is available to drive the oil motor?
This is followed by the selection of the exact motor type. - Is a leakage oil connection possible?
In some applications there is simply no space to implement an additional oil connection. If the technical data of the motor is taken into account, operation without a leakage oil connection is possible. - Should several motors be connected in parallel or in series?
Depending on the circuit, there are a few important points to consider. - What oil temperatures can be expected?
At temperatures above 80°, for example, VITON seals are required. - Which hydraulic fluid should the motor be operated with?
The use of hydraulic media such as HFC liquids or bio-oils may have an impact on the sealing material to be selected or the service life of the hydraulic motor. - What is the surrounding medium like?
If the hydraulic motor is used in salty air (e.g. on ships, salt spreaders or road sweepers), a special paint finish is recommended to protect the motor from corrosion
Other important criteria are the available installation space, flange and shaft shape, if a speed measurement is necessary, is the motor used to hold (brake motor) etc
If you have any questions about the design or the right choice, please do not hesitate to contact us.
Advantages and disadvantages of gerotor motors
benefits
- Orbital motors are low-speed hydraulic motors . Speeds of up to approx. 1500 rpm can be reached
- High pressure resistance , sometimes up to 400 bar (heavy-duty version)
- Very well suited for hydrostatic travel drives
- Can be used in open or closed hydraulic circuits (with additional flushing valve)
- Smooth running over the entire speed range
- Constant operating torque over a wide speed range
- High starting torque
- High return pressure without using a drain line
- High efficiency
- Long service life , even under extremely tough operating conditions
- Robust and compact construction
- Large radial and axial bearing load capacity
- Relatively cheap design
- Many different flange and shaft designs available
disadvantage
- Depending on the design, only suitable for speeds up to a maximum of 1500 rpm
- Poor efficiency at very low speeds
- Few or no adjustment options (regulation usually only possible with external components)
You can also find oil motors in our hydraulic shop!
We carry our own brand of gerotor motors as well as those from M+S Hydraulics, one of the leading manufacturers of orbital motors.