Brugger value
This value is actually only known to die-hard hydraulic engineers, the Brugger value. But what does this value say?
The minimum requirements for hydraulic and gear oils are firmly defined in DIN standards. However, they do not ensure the trouble-free operation of certain equipment in all cases. This applies in particular to slow-running, shock-loaded gearboxes, vane pumps, threaded couplings, bed ways and steel/bronze pairings in plain bearings. Often the load capacity of the oil used is not sufficient. In order to clearly analyze the load capacity of the lubricant, the practical Brugger test was developed.
Parker Hannifin’s official definition states that mixed friction always occurs in hydraulic components because the sliding speeds between friction partners are often below the limit for the reliable build-up of a hydrodynamic lubricating film. In the case of mixed friction, i.e. when the components are in direct metallic contact, the lubricity is the decisive factor. The lubricity is measured according to DIN/EN 51 347 and given as a permissible specific load in N/mm² at which no wear occurs on the sliding partners. This value is sometimes also referred to as the “Brugger value”.
For general applications, this value must be at least 30 N/mm², measured according to DIN 51 347-2. In dynamically highly loaded systems and machines with rapid load changes (frequent pressure changes between low and high operating pressures, high-speed presses, plastics machines, etc.), fluids with a value not below 50 N/mm², measured according to DIN 51 347-2, should be used.
What can happen in a hydraulic system if the Brugger value of the hydraulic oil used does not reach the recommended minimum value? Due to the insufficient lubricating film, the lubricity between the components moving on each other is no longer sufficient, which leads to damage of the components. The consequences are material abrasion, which in the worst case can damage the entire hydraulic system.
How is it tested?
At the heart of the tester are two rotationally symmetrical test specimens whose axes are offset by 90° relative to each other. The lower test specimen is a ring with an outer diameter of 25 mm. It is mounted on a shaft which is driven by a three-phase motor via a toothed belt drive. It rotates at 960 rpm ±5% at idle and drops to a maximum of 860 rpm under load.
The upper test specimen is a cylinder with a diameter of 18 mm. It is firmly clamped in a rotating holder and is pressed by this against the rotating test ring by a weight. The sliding speed is 1.2 m/s.
Both the shaft of the test ring and the pivot points of the levers are mounted on anti-friction bearings. Now the test ring is doused with the lubricant to be tested. The test cylinder is pressed against the test ring with 400 N. The drive of the test ring starts under load. The test duration is 30 seconds.
Depending on the lubricant property, the rotating test ring generates a wear surface of varying size on the stationary test cylinder. The wear surface has the shape of an ellipse. The main axes of the ellipse are measured with a measuring magnifier. From this, the projection area of the wear surface is calculated. The quotient of the contact force and the projected wear surface is given as the load capacity of the lubricant according to Brugger B (N/mm2).
To obtain reproducible results, the same initial conditions must always be created. Since several tests are carried out with one test ring, the test ring and cylinder must each be washed with SBP petrol. The surfaces must not show any traces of residues from the previous test visible to the naked eye. Make sure that the test ring never falls below the diameter of 24.5 mm. Testing in the mixed friction area with the Brugger lubricant tester is specified in DIN 51347-1.
Expressiveness and reliability
The test procedure according to Brugger currently provides the only decision-making basis for a correct lubricant selection with regard to lubricant load capacity. A large number of measurements have shown that the reproducibility of the results is good. Scatter is ± 10% of the measured values.
Source: https://www.oelcheck.de/wissen-von-a-z/pruefverfahren-und-geraete/brugger-test-belastbarkeit-von-schmierstoffen-oelchecker-sommer-2003.html
You prefer to go shopping right away?
In our hydraulic store you will find a oils and lubricants
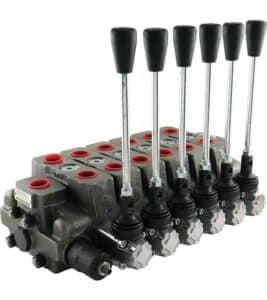
Mobile control block
In the field of mobile machinery, there are special requirements for valve technology. Control blocks for mobile applications have significant differences to hydraulic valves in
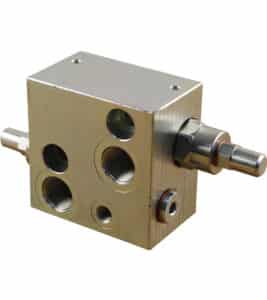
Hydraulics lowering brake valves
Hydraulic lowering brake valves – safety device in hydraulic systems Counterbalance valves are hydraulic valves consisting of pilot-operated check valves and associated throttling and damping

axial piston engines
Axial piston motors – for high speeds Functionality of axial piston motors Axial piston motors are based on the basic principle of an axial piston

Calculate hydraulic line
Content Calculate hydraulic line: step-by-step guide for accurate calculation Hydraulic lines are an important component of hydraulic systems and are used to transfer pressurized fluids.

Manual hydraulic hose press
How to press a hydraulic hose with a manual hydraulic hose press? In our video you will also find step by step instructions In 7

How do hydraulics work?
Hydraulics is a fascinating principle that is used in many areas of technology. But how exactly do hydraulics work and what are they used for?
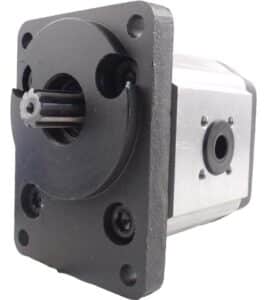
Gear motors
Hydraulic gear motor – high speed at low price What is a gear motor? Gear motors are hydraulic motors in their constructional design of a

Calculate hydraulic motors
Calculation of sip volume, flow rate and rotational speed Calculate swallowing volume Calculate hydraulic motors – In the first case of the calculation the flow

Hydraulic motors in series
What should be considered when hydraulic motors are connected in series? Series connection of Hydraulic motors are used when a constant high speed is required
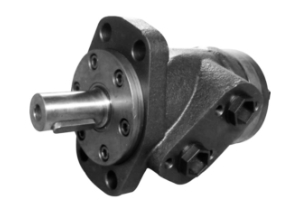
gerotor motors
Gerotor motor, oil motor, planetary motor – low-speed hydraulic motors Content How does a gerotor motor or oil motor work? The so-called gerotor motors (also

Hydraulic motors parallel circuit
What should be considered when connecting hydraulic motors in parallel? Parallel connections of Hydraulic motors are used when you need a high torque in the
Hydraulic filter – task and function
Task of hydraulic filters To ensure trouble-free operation in hydraulic systems, the use of hydraulic filters is essential.Practice shows that about 80% of all premature
- Mobile control block - 13. May 2023
- Hydraulics lowering brake valves - 6. May 2023
- axial piston engines - 2. May 2023